Volba povrchové úpravy je problém, se kterým se potýká každý designér.K dispozici je mnoho druhů povrchových úprav a designér na vysoké úrovni by měl zvážit nejen hospodárnost a praktičnost provedení, ale také věnovat pozornost procesu montáže a dokonce i ekologickým požadavkům.Níže je uveden stručný úvod k některým běžně používaným povlakům spojovacích prvků založených na výše uvedených principech, pro odborníky na spojovací materiály.
1. Elektrogalvanizace
Zinek je nejběžněji používaný povlak pro komerční spojovací prvky.Cena je relativně nízká a vzhled je dobrý.Mezi běžné barvy patří černá a vojenská zelená.Jeho antikorozní výkon je však průměrný a jeho antikorozní výkon je nejnižší mezi vrstvami zinkování (nátěru).Obecně platí, že neutrální solný test pozinkované oceli se provádí do 72 hodin a používají se také speciální těsnicí prostředky, aby se zajistilo, že neutrální solný test trvá déle než 200 hodin.Cena je však drahá, což je 5-8krát vyšší než u běžné pozinkované oceli.
Proces elektrogalvanizace je náchylný k vodíkové křehkosti, takže šrouby vyšší než 10,9 nejsou obecně galvanizovány.Přestože lze vodík odstranit pomocí pece po pokovování, pasivační film se poškodí při teplotách nad 60 ℃, takže odstranění vodíku musí být provedeno po galvanizaci a před pasivací.To má špatnou provozuschopnost a vysoké náklady na zpracování.Ve skutečnosti obecné výrobní závody aktivně neodstraňují vodík, pokud to nepožadují konkrétní zákazníci.
Konzistence mezi utahovacím momentem a silou před utažením pozinkovaných spojovacích prvků je špatná a nestabilní a obecně se nepoužívají pro spojování důležitých součástí.Aby se zlepšila konzistence momentového předpětí, může být také použita metoda nanášení mazacích látek po pokovení ke zlepšení a posílení konzistence momentového předpětí.
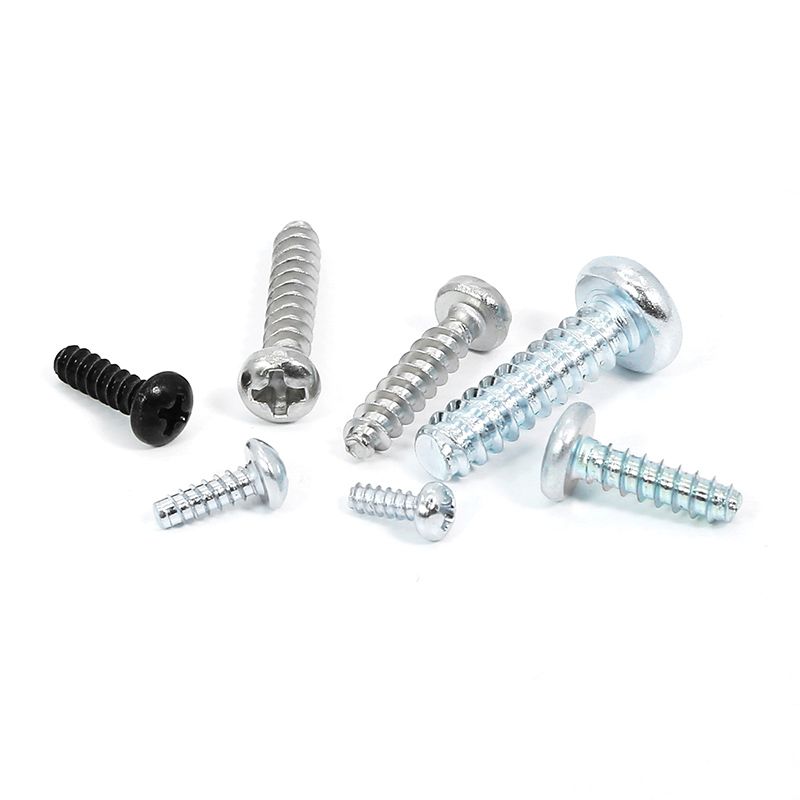
2. Fosfátování
Základní zásadou je, že fosfátování je relativně levnější než galvanizace, ale jeho odolnost proti korozi je horší než galvanizace.Po fosfátování by měl být aplikován olej a jeho odolnost proti korozi úzce souvisí s výkonem použitého oleje.Například po fosfátování, nanesení obecného antikorozního oleje a provedení testu neutrální solné mlhy po dobu pouze 10-20 hodin.Aplikace vysoce kvalitního oleje proti korozi může trvat až 72-96 hodin.Jeho cena je však 2-3krát vyšší než u běžného fosfátovacího oleje.
Existují dva běžně používané typy fosfátování pro spojovací prvky, fosfátování na bázi zinku a fosfátování na bázi manganu.Fosfátování na bázi zinku má lepší mazací výkon než fosfátování na bázi manganu a fosfátování na bázi manganu má lepší odolnost proti korozi a opotřebení než zinkování.Může být použit při teplotách v rozmezí od 225 do 400 stupňů Fahrenheita (107-204 ℃).Zejména pro připojení některých důležitých komponent.Jako jsou šrouby a matice ojnice motoru, hlavy válců, hlavního ložiska, šrouby setrvačníku, šrouby a matice kol atd.
Vysokopevnostní šrouby používají fosfátování, které také může zabránit problémům s vodíkovou křehkostí.Proto šrouby vyšší než 10,9 v průmyslové oblasti obecně používají fosfátovací povrchovou úpravu.
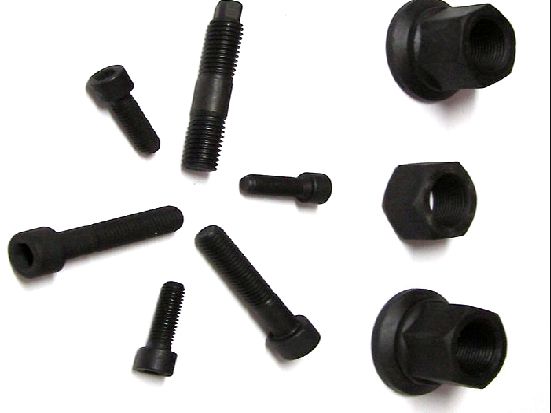
3. Oxidace (černání)
Černění+olejování je oblíbený nátěr pro průmyslové spojovací prvky, protože je nejlevnější a vypadá dobře před spotřebou paliva.Díky svému zčernání nemá téměř žádnou antikorozní schopnost, takže bez oleje rychle zreziví.I v přítomnosti oleje může test solnou mlhou trvat pouze 3-5 hodin.
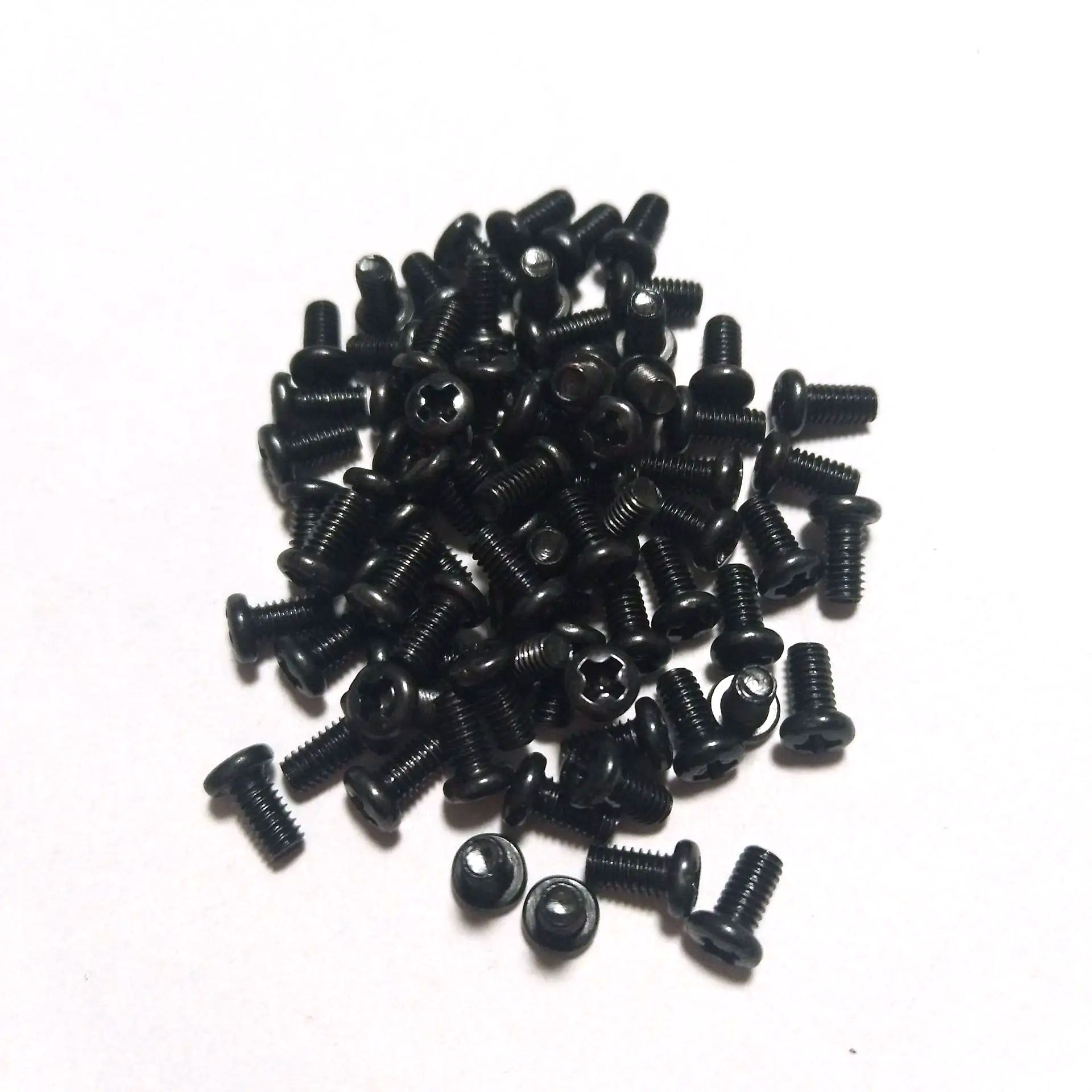
4. Galvanizační přepážka
Kadmium má vynikající odolnost proti korozi, zejména v mořském atmosférickém prostředí, ve srovnání s jinými povrchovými úpravami.Náklady na zpracování odpadních kapalin v procesu galvanického pokovování kadmiem jsou vysoké a jeho cena je asi 15-20krát vyšší než cena galvanického pokovování zinkem.Nepoužívá se tedy v obecných průmyslových odvětvích, pouze pro specifická prostředí.Spojovací prvky používané pro plošiny pro těžbu ropy a letadla HNA.
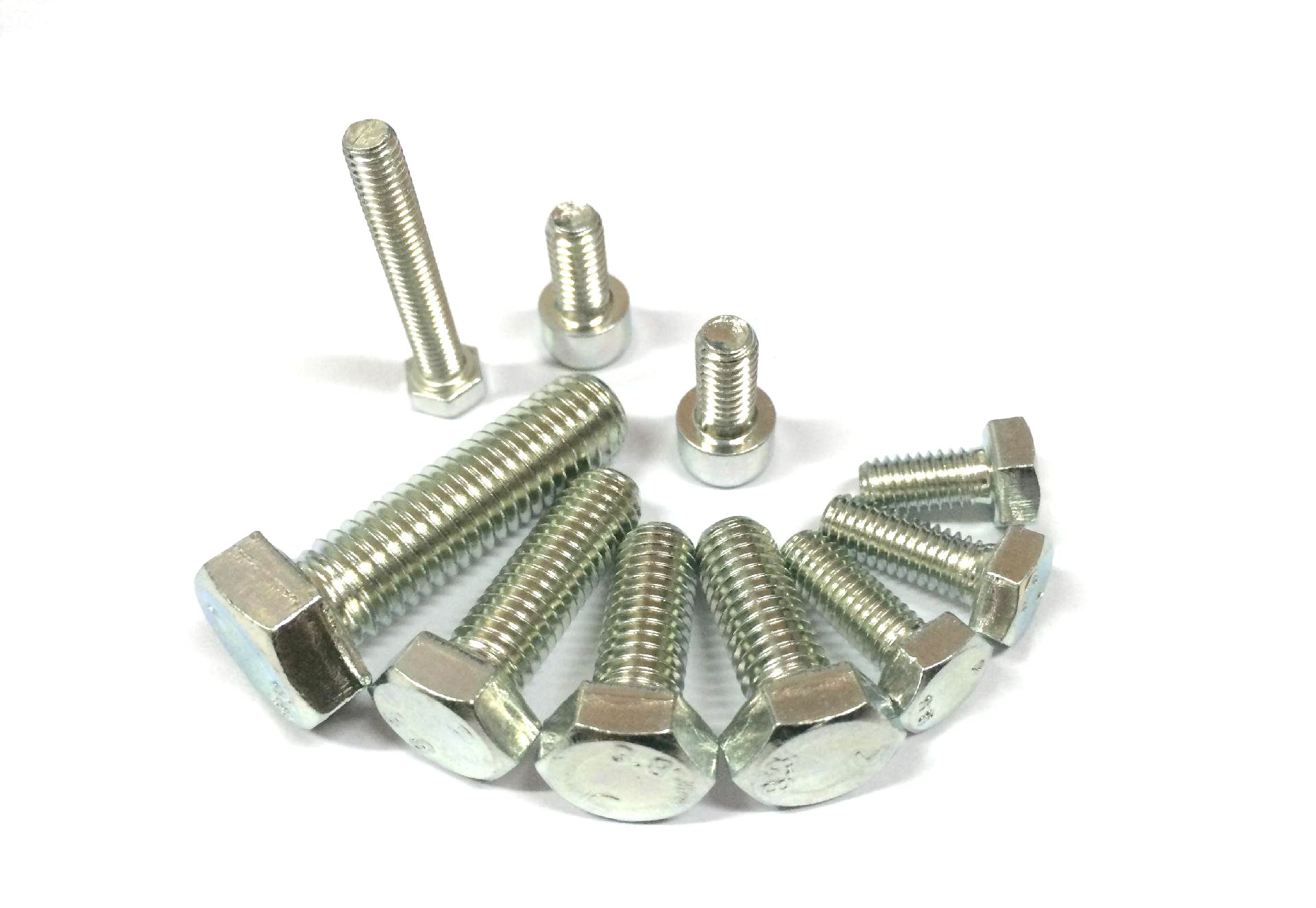
5. Chromování
Chromový povlak je velmi stabilní v atmosféře, není snadné měnit barvu a ztrácet lesk a má vysokou tvrdost a dobrou odolnost proti opotřebení.Použití chromování na spojovacích prvcích se obecně používá pro dekorativní účely.Zřídka se používá v průmyslových oblastech s vysokými požadavky na odolnost proti korozi, protože dobré pochromované spojovací prvky jsou stejně drahé jako nerezová ocel.Pouze pokud je pevnost nerezové oceli nedostatečná, používají se místo toho chromované spojovací prvky.
Aby se zabránilo korozi, měly by být měď a nikl před chromováním nejprve pokoveny.Chromový povlak odolá vysokým teplotám 1200 stupňů Fahrenheita (650 ℃).Je tu ale také problém vodíkového křehnutí, podobně jako u galvanizace.
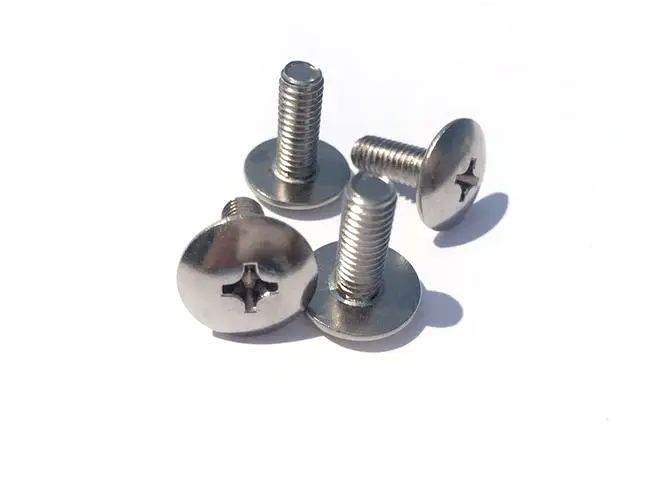
6. Niklování
Používá se hlavně v oblastech, které vyžadují antikorozní ochranu a dobrou vodivost.Například výstupní svorky akumulátorů vozidel.
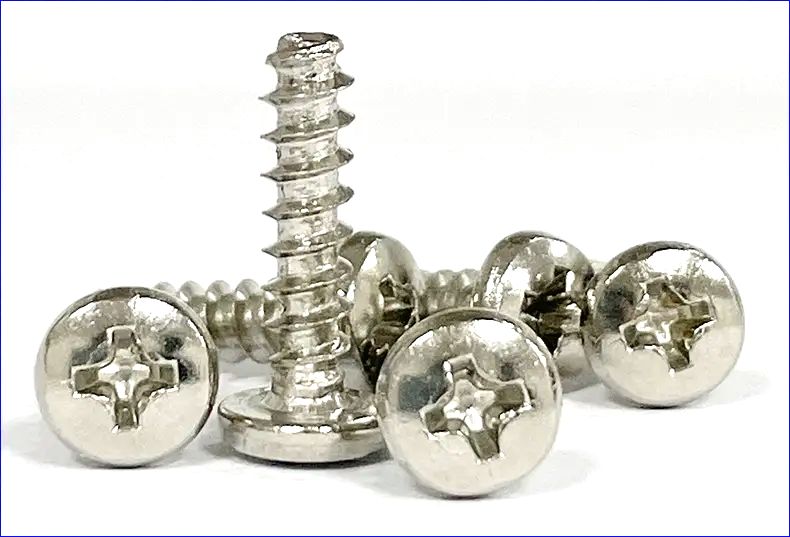
7. Žárové zinkování
Žárové zinkování je tepelně difúzní povlak zinku zahřátý na kapalinu.Tloušťka povlaku se pohybuje mezi 15 a 100 μm.A není snadné jej ovládat, ale má dobrou odolnost proti korozi a často se používá ve strojírenství.Během procesu žárového zinkování dochází k silnému znečištění, včetně zinkového odpadu a zinkových par.
Kvůli silnému povlaku způsoboval potíže při šroubování vnitřních a vnějších závitů v upevňovacích prvcích.Vzhledem k teplotě zpracování žárovým zinkováním jej nelze použít pro spojovací prvky vyšší než 10,9 (340~500 ℃).
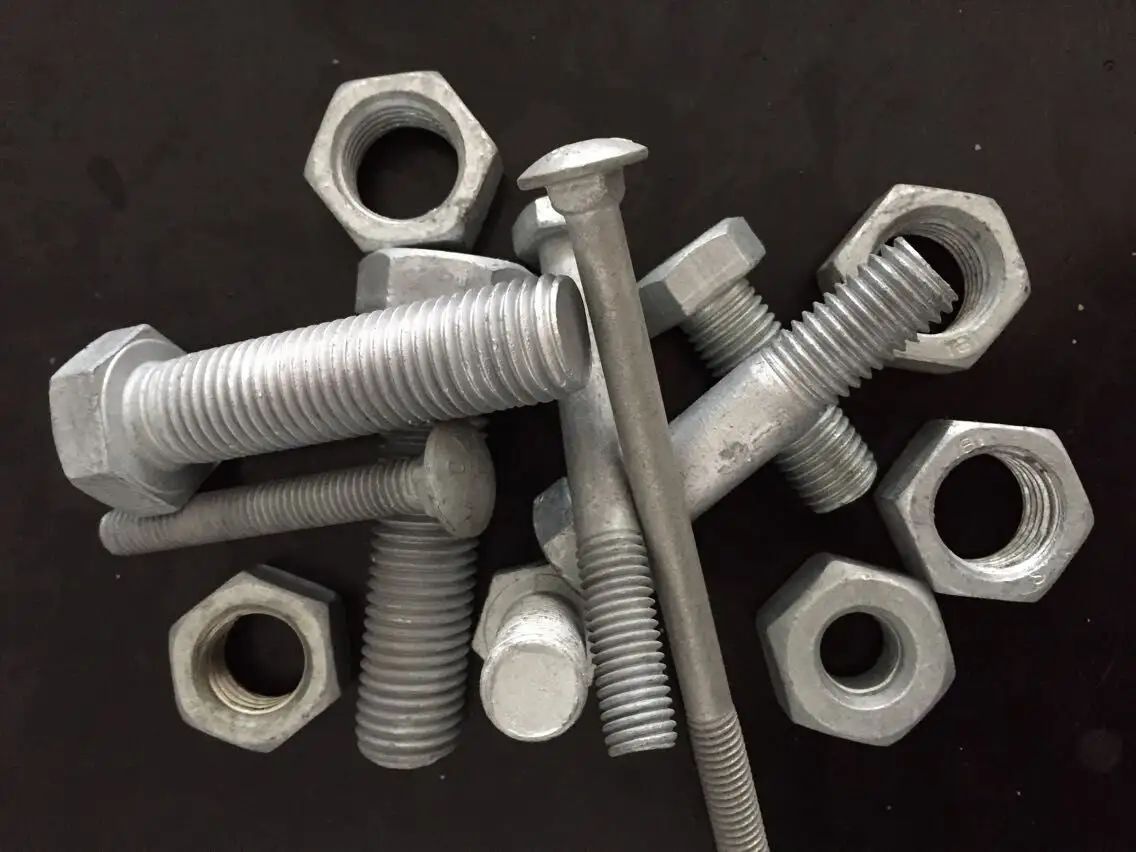
8. Infiltrace zinku
Zinková infiltrace je pevný metalurgický tepelně difúzní povlak zinkového prášku.Jeho rovnoměrnost je dobrá a stejnoměrnou vrstvu lze získat jak v závitech, tak ve slepých otvorech.Tloušťka pokovení je 10-110 μm.A chyba může být kontrolována na 10%.Jeho pevnost spojení a antikorozní vlastnosti s podkladem jsou nejlepší u zinkových povlaků (jako je elektrogalvanizace, žárové zinkování a Dacromet).Proces jeho zpracování je bez znečištění a nejšetrnější k životnímu prostředí.
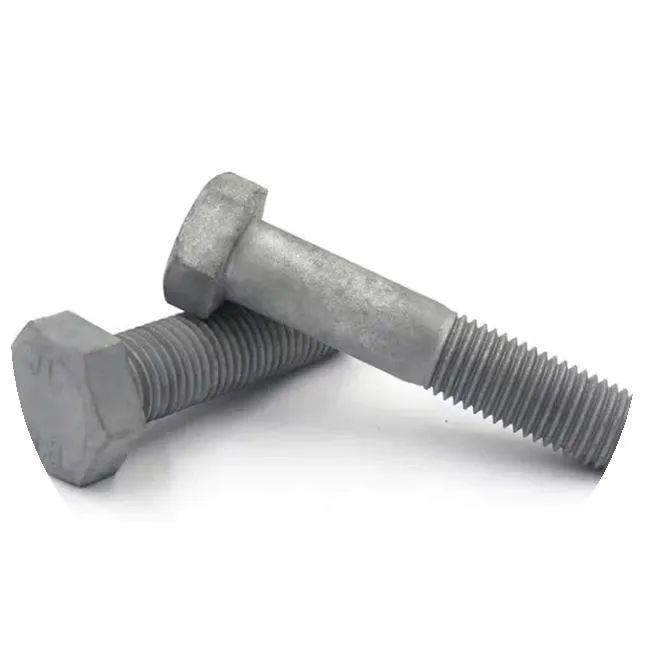
9. Dacromet
Neexistuje žádný problém s vodíkovou křehkostí a konzistence předpětí točivého momentu je velmi dobrá.Bez ohledu na otázky chrómu a životního prostředí je Dacromet ve skutečnosti nejvhodnější pro vysoce pevné spojovací prvky s vysokými požadavky na ochranu proti korozi.
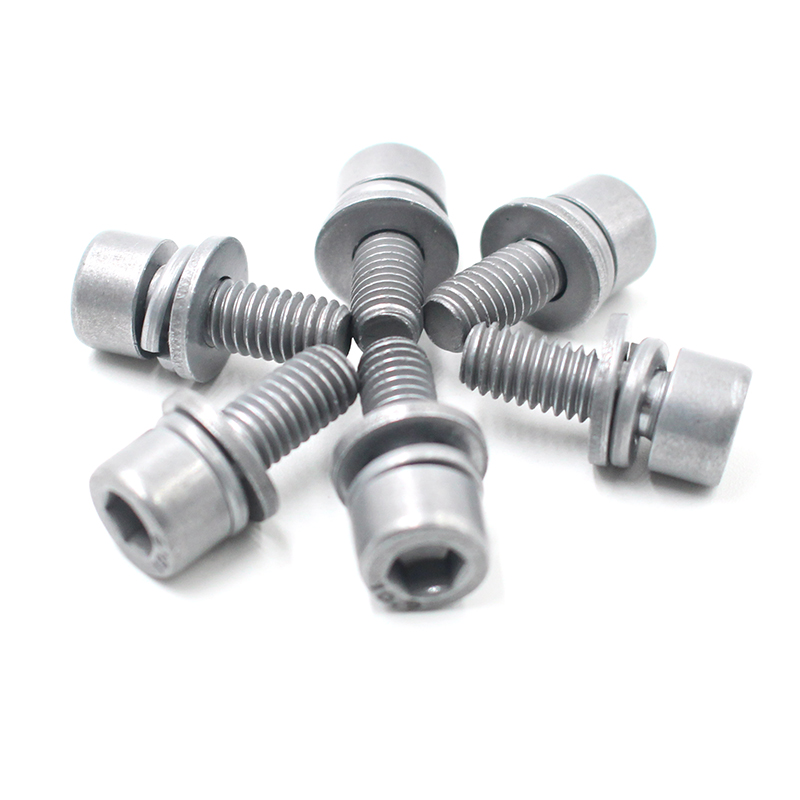
Čas odeslání: 19. května 2023